Contributing to smaller sizes and higher performance of electronic devices
Bando Chemical
Thermal Management
Heat is the primary factor impeding smaller sizes and higher performance of electronic devices.
The dispersion technologies and materials processing technologies of Bando Chemical are the solution.
Developed products using Bando Chemical thermal management technologies
What is Bando Chemical
thermal management?
The need for thermal management
The demands for smaller sizes and higher performance of electronic devices have been growing in a wide range of fields due to the increasing power of power devices in fields such as automobiles, railways, and new energy, and also due to the full-scale use of these devices in the IoT and edge computing telecommunications industries.
Background behind smaller sizes and higher performance of electronic devices
-
Smaller sizes
- Heat accumulation due to higher density
- Difficulty in installing heat dissipating mechanisms
- Larger area of heat effects on nearby parts
-
Higher performance
- More heat generation due to higher processing loads
- Restrictions on parts that can be used due to heat resistance requirements
- Increasing requirements for performance and reliability
Active thermal control is essential in order to meet the increasing requirements for smaller sizes and higher performance.
Position of Bando Chemical
For effective thermal management, in addition to a compact thermal design, more advanced functions of the electronic materials that comprise the components are also essential. Bando Chemical has achieved more advanced functions of electronic materials by applying the wide range of materials technologies that we have developed over many years.
Development and supply of electronic material products to meet demands for thermal design and total design under increasingly harsh conditions
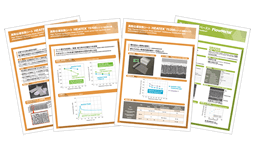
Download the Bando Chemical catalog of products supporting smaller sizes and higher performance of electronic devices.
・HEATEX®high thermal conductivity sheet
・FlowMetal®silver nanoparticle bonding material paste
Why is Bando Chemical engaged in thermal management?
The use of Bando Chemical core technologies such as rubber and elastomer processing technologies developed from our dispersion technologies has allowed us to successfully meet the needs of large numbers of customers. In addition, the combination of orientation technologies and nanoparticle production technologies has made it possible for us to produce electronic materials that are ideal for thermal management.
- Bando Chemical thermal managementOptimization and improving the function of electronic materials necessary for electronic devices
- Required technologiesTechnologies for control of compound materials
- Technologies possessed by Bando Chemical
- Dispersion technologies that allow stable use of material characteristics
- Rubber, elastomer, and other material processing technologies
- Orientation technologies to control the properties of materials that have directionality
- Nanoparticle production technologies that expand the range of nanoparticle applications
Resolving issues in electronic device manufacturing by developing and manufacturing unique products applying the technologies that we have developed over our history of more than 100 years
In the thermal management field, increasing the heat dissipation effects makes it possible to develop products that can suppress heating.
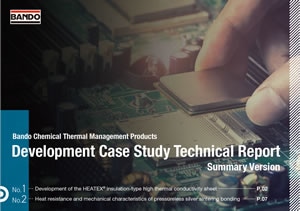
If you would like to know more about the advanced technical capabilities of Bando Chemical,download the Technical Report.
DownloadCharacteristic products provided by Bando Chemical
We bring together the Bando Chemical core technologies to develop unique products such as the following to resolve our customers’ issues.
Achieving superior heat resistant reliability and effective heat transmission
-
- Customers who are searching for a thermally conductive sheet with high thermal conductivity that can support increasing amounts of heat generated per unit of surface area
- Customers who want a thermally conductive sheet with little performance changes in high temperature environments
- Customers who require a heat dissipating material with high workability
High thermal conductivity sheet
Click here for datasheet Click here for Detail
HEATEX® -
- Customers who are looking for a bonding material with high heat resistance that can be used in higher temperature ranges
- Customers who want a bonding material that has high thermal conductivity and low electrical resistance
- Customers who want to simplify the manufacturing process with pressureless bonding
Silver nanoparticle bonding material paste
Click here for datasheet Click here for Detail
FlowMetal®
Achieving ultra-high thermal conductivity with a boron nitride heat-conducting filler
High thermal conductivity sheet
HEATEX®
Click here for datasheet
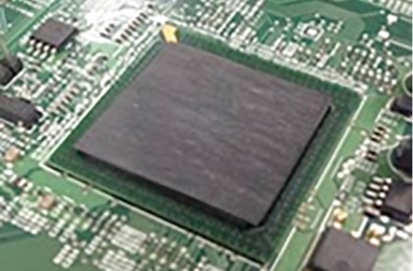
Provides both ultra-high thermal conductivity and high heat resistance.
Boron nitride with high thermal conductivity in the axial direction is used as the heat-conducting filler. By orienting it in the sheet thickness direction, we have achieved a high thermal conductivity of 17 W/mK. Silicone rubber is used as the base, providing the characteristic flexibility and excellent heat resistance of rubber.
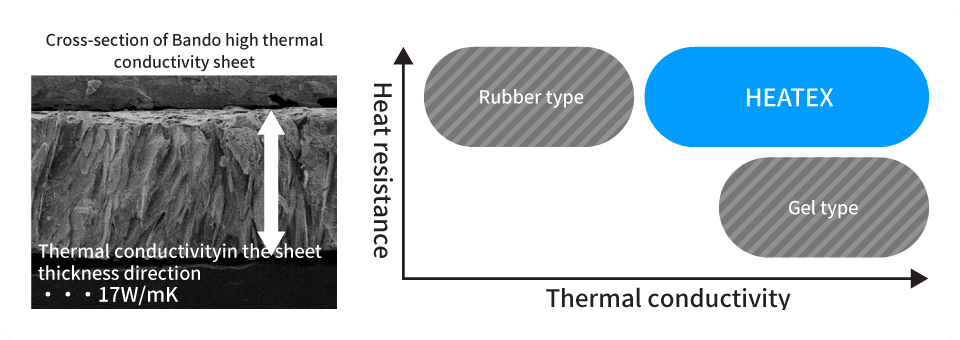
Surface properties (adhesive or non-adhesive) and flexibility can be selected according to the purpose.
Because it is in a strong sheet form, this product can be easily processed and worked into a variety of shapes. The surface properties (adhesive or non-adhesive) and flexibility can be selected according to the purpose. (The adhesive and flexible types are currently under development.)
The lineup includes an electrically conductive type as well as an insulation type.
In addition to the insulating, high thermal conductivity type that uses boron nitride filler, the lineup also includes a high thermal conductivity, electrically conductive type. These can be used to achieve high thermal conductivity in a range of applications.
Examples of HEATEX®applications
- As an insulating, thermally conductive material between a circuit board and heat sink
- As a thermally conductive material for temperature sensors or similar devices
- As a heat dissipating measure for power devices and a wide range of electronic components
Low-temperature bonding & high heat resistance bonding material achieved with low temperature sintered silver nanoparticles
Silver nanoparticle bonding material
FlowMetal®
Click here for datasheet
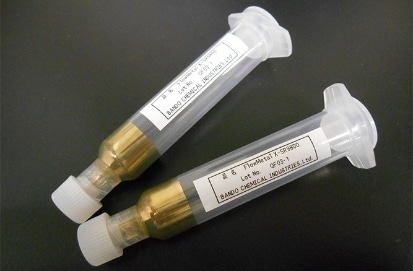
Achieves both low bonding temperature and high heat resistance.
This bonding material uses silver nanoparticles that are capable of low temperature sintering. With conventional solder and similar materials, it was necessary to use the devices at or below the bonding temperature. However this bonding material has heat resistance that allows it to be used with no problems even in high temperature environments that exceed the bonding temperature.
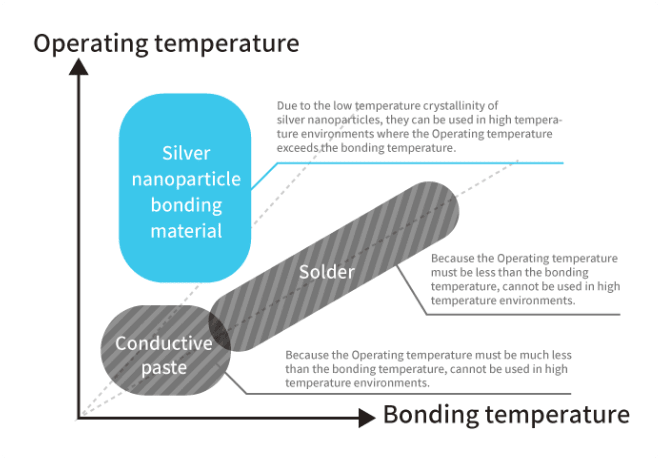
Capable of bonding without pressure
The same durability and heat resistance as when pressure is applied can now be achieved with pressureless bonding. Because the pressure application process is not necessary, the manufacturing process can be simplified, helping reduce costs and the number of processes.

The lack of the pressure load on substrates and components which occurs during pressure application also contributes to stabilizing the quality of manufactured electronic components.
* Depending on the bonding conditions, pressureless bonding may not be suitable in some cases.
* A lineup of materials that can also be used for pressure bonding is available.
Provides both high thermal conductivity and low electrical resistance.
Achieves both high thermal conductivity and low volume (electrical) resistivity, something that was not possible with previous bonding materials. This supports both electrical conduction and heat dissipation without problems when bonding a power device or other chip that has a high withstand voltage and large current.
Examples of FlowMetal®applications
- For bonding of power devices or other chips with high withstand voltage and large current
- As a (lower cost) substitute for gold-tin solder when bonding LED, laser diodes, or Peltier elements
- For bonding of ECU and other automobile components, communication devices, robot controllers, and similar parts