High positioning accuracy" means
In Japan, the decrease in the working population will require more labor savings on production lines than ever before, and industrial robots are expected to become even more widespread in this context. Industrial robots are required to perform a series of repetitive motions, and their driving parts must have a high degree of positioning accuracy.
High positioning accuracy" in the transmission mechanism means that when the driving pulley on the drive side makes one rotation or reciprocating rotation, the driven pulley on the driven side also makes the same number of revolutions (same position).
The graph below shows the results of a test using an encoder to measure the rotational speed of the driving pulley (blue line) and driven pulley (red line) in the process of increasing the speed to 40 m/sec from the start of belt drive in a synchronous belt drive. The difference between the rotational speeds of the driving pulley and the driven pulley is called the phase difference. As can be seen from the graph, when the driving pulley starts to rotate, the driven pulley starts to move via the belt, but there is a slight delay because of the elasticity of the belt. The belt is elastic, so there is a slight delay. After that, the driving pulley side is pulled by the belt, and an overshoot that exceeds the driving pulley rpm may occur. The difference (area) between the driving pulley (blue line) and the driven pulley (red line) is one of the indicators of response, and the smaller this area is, the faster the motor can respond to the motor output and transmit force to the driven side, thereby improving the positioning accuracy of the machine. The smaller this area is, the faster the motor can respond to the output and transmit force to the driven side.
In mechanisms such as industrial robots that require rapid acceleration, sudden stop, and reciprocating rotation, changes in rotation speed cycles occur frequently in a short period of time, and this phase difference greatly affects the positioning accuracy of the machine. In this article, we define "less phase difference = better response and positioning accuracy," and explain the recommended transmission mechanisms and product selection points to achieve a high level of positioning accuracy.
Recommended transmission mechanism for advanced positioning accuracy
Then, what kind of transmission mechanism should be selected to achieve high positioning accuracy? We have compiled a list of features for each of the transmission mechanisms commonly used in machine drives: "synchronous belt," "chain," "ball screw," and "linear drive.
The above table shows that "synchronous belt" is the transmission mechanism with the most excellent features. Many people may have the impression that "linear drive" and "ball screw" are superior from the viewpoint of positioning accuracy. However, price, design flexibility, and ease of maintenance may often be barriers to considering their introduction. Synchronous belt and chain drives, on the other hand, offer cost advantages and a high degree of design freedom, making it easy to consider their introduction. Chains have the disadvantages of being made of metal, being heavy, noisy, and requiring lubrication. In comparison, the synchronous belt is the best transmission mechanism for machines that require a high degree of positioning accuracy.
Even after this explanation, some people may still have a negative impression of synchronous belts, saying that the positioning accuracy under high loads is inferior to that of a metal transmission mechanism, if the elasticity of the belt is such that it is a synchronous belt. However, the recent evolution of the synchronous belt makes it unwise not to include it as an option in machine design. As technology evolves, high-load synchronous belts are being developed.
What are the factors that affect the positioning accuracy of synchronous belts?
cord

The most significant factor affecting the phase difference is the modulus of elasticity of the cord. The belt has a member called a "cord" that transmits power, and a cord with low elongation (high modulus of elasticity) improves response and reduces the phase difference.
①synchronous belt cord
The following graph compares the phase difference between a glass cord (orange line), which is often used as a general synchronous belt cord, and a carbon cord (gray line), which has the feature of high modulus of elasticity. It can be seen that the run-out width of the carbon cord is smaller than that of the glass cord when it starts to drive. In other words, the carbon cord can respond to the motor output more quickly and transmit power to the driven side, leading to a smaller accumulation of final misalignment.
Backlash
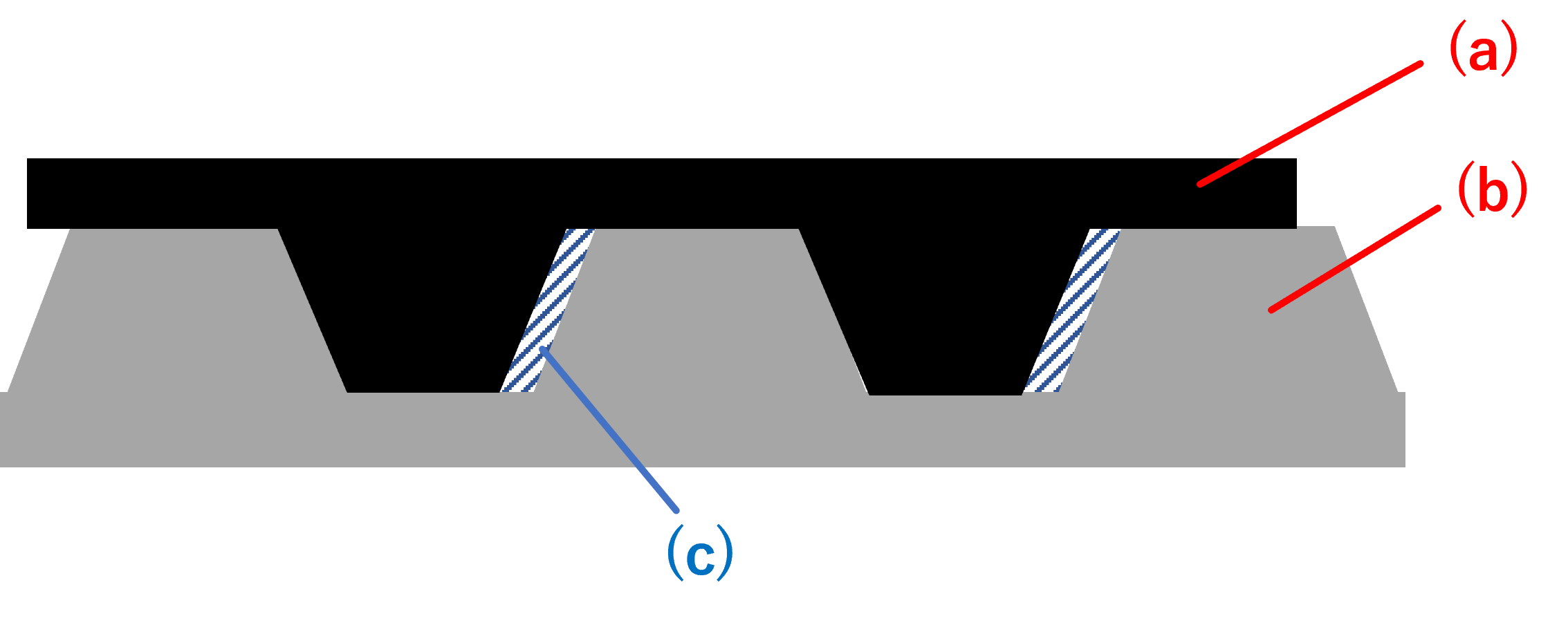
The amount of backlash is another factor that affects positioning accuracy. backlash refers to the gap between the pulley tooth and the belt tooth, and the amount of this gap is called the "backlash amount, If the backlash is large, there will be a time difference in the rotation of the driving pulley and the driven pulley when the belt is started or when it rotates in reverse. Therefore, to improve positioning accuracy, the amount of backlash should be as small as possible.
*(a) Belt (b) Pulley (c) Backlash
The most important factor that determines the amount of backlash is the belt tooth shape. synchronous belt tooth shapes are mainly classified into "trapezoidal tooth", "arc tooth", and "triangular tooth".
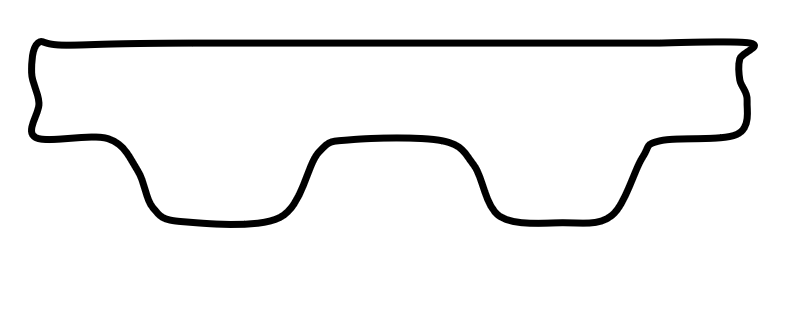
Trapezoidal tooth" is a tooth shape developed in the early days of synchronous belts, which has a large amount of backlash with the pulley during engagement, resulting in relatively low positioning accuracy during forward and reverse operation.
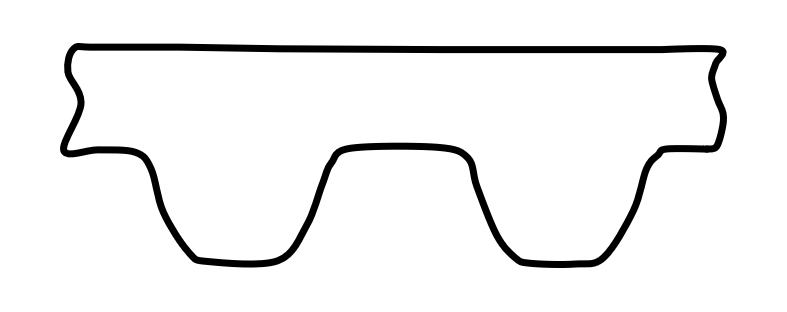
The "arc tooth" is a tooth shape designed for higher positioning accuracy, higher load capacity, and longer life. The arc shape makes engagement smoother and reduces backlash. These two effects improve positioning accuracy.
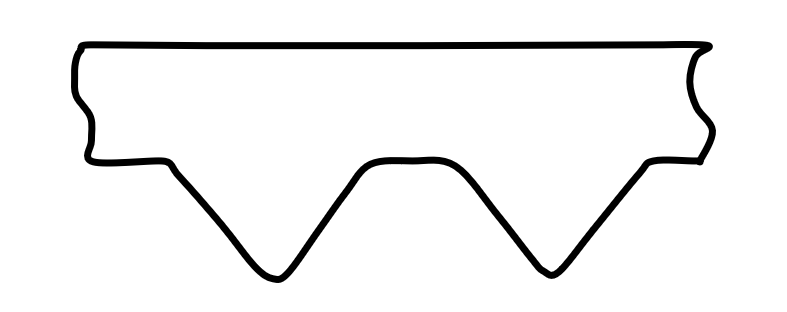
In the "triangular tooth" type, the belt always engages with the pulley by contacting both stress surfaces, resulting in zero backlash. However, this type is often used for applications that require high positioning accuracy, light loads, and relatively small load fluctuations, as it is highly likely to cause missing teeth, jumping, and other failures under heavy loads.
What is the best belt for high-precision positioning?
You may have understood from the previous explanations that a belt with a high elasticity cord and a circular arc tooth shape is optimal for reducing phase differences under high load and load fluctuation conditions.
And the synchronous belt that satisfies these conditions is Bando Chemical's top-of-the-line, high-load synchronous belt Ceptor®-X.
Ceptor®-X uses a high-elasticity carbon cord, which provides better response and smaller phase difference. In addition, the "Stooth type" is used, which has a large transmission capacity among arc toothes.
Ceptor®-X is the belt of choice for those who require a high degree of long-term positioning accuracy under heavy loads.
Furthermore, the improved transmission capacity per width has the advantage of making the belt width 40% narrower than that of our HP-STS, which is a standard stooth type under the same conditions. This reduces the weight and space of the belt and the pulley that receives it, leading to both high positioning accuracy and lightweight, space-saving machines.
Ceptor®-X is mainly used in various applications such as industrial robots, medical and pharmaceutical equipment, semi-conductor manufacturing equipment, and injection molding machines. Please refer to the bottom of this page for detailed applications and examples.
summary
We have explained the definition of positioning accuracy in transmission mechanisms and the recommended synchronous belt Ceptor®-X for achieving a high level of positioning accuracy. If you are interested in achieving high positioning accuracy in mechanisms that are subject to high loads, please consider Bando Chemical's Ceptor®-X. If you have any questions, please feel free to contact us.