'높은 위치 결정도'는 무엇인가요?
앞으로 노동 인구의 감소로 인해 생산 라인의 자동화가 더욱이 필요하며, 이러한 맥락에서 산업용 로봇이 널리 보급될 것으로 예상됩니다. 산업용 로봇은 일련의 반복적인 동작을 수행해야 하며, 구동부는 높은 수준의 위치 결정도를 필요로 합니다.
전동 메커니즘에서의 "높은 위치 결정도"란 구동 측의 구동 풀리가 1회전 또는 왕복 회전을 할 때, 종동 측의 종동 풀리도 같은 수의 회전(동일한 위치)을 하는 것을 의미합니다.
아래 그래프는 타이밍 벨트 구동에서 벨트 구동 시작부터 속도를 40m/sec로 높이는 과정에서 구동 풀리(파란색 선)와 종동 풀리(빨간색 선)의 회전수를 인코더를 사용하여 측정한 테스트 결과입니다. 구동 풀리와 종동 풀리의 회전 속도 차이를 위상차라고 합니다. 그래프에서 알 수 있듯이 구동 풀리가 회전하기 시작하면 종동 풀리는 벨트를 통해 움직이기 시작하지만 벨트의 탄성으로 인해 약간의 지연이 발생합니다. 또한 종동 풀리 측이 벨트에 의해 당겨져 구동 풀리의 rpm을 초과하는 오버슈트가 발생할 수 있습니다. 구동 풀리(파란색 선)와 종동 풀리(빨간색 선)의 차이(면적)는 응답성을 나타내는 지표 중 하나이며, 이 면적이 작을수록 모터 출력에 더 빨리 응답하며 종동 측에 힘을 전달하여 기계의 위치 정확도를 향상시킬 수 있습니다. 이 면적이 작을수록 모터의 출력에 더 빨리 반응하여 종동 측에 힘을 전달할 수 있기 때문에 위치 결정도 향상이 가능합니다.
산업용 로봇과 같이 빠른 가속, 급정지, 왕복 회전이 필요한 기구에서는 단시간에 회전 속도 주기의 변화가 빈번하게 발생하며, 이러한 위상차는 기계의 위치 결정도에 큰 영향을 미칩니다. 본 작성물에서는 "위상차가 적을수록 응답성과 위치 정확도가 좋아진다"고 정의하고, 높은 수준의 위치 결정도를 달성하기 위해 권장되는 전동 기구와 제품 선택 포인트를 설명합니다.
높은 위치 결정도를 실현하기 위한 권장 전동 메커니즘
높은 위치 결정도를 달성하기 위해 어떤 전동 메커니즘을 선택해야 할까요? 기계 구동에 일반적으로 사용되는 각 전달 메커니즘에 대한 기능 목록을 작성했습니다. "타이밍 벨트", "체인", "볼 스크류" 및 "리니어 구동"입니다.
위의 표는 "타이밍 벨트"가 가장 우수한 기능을 가진 전달 메커니즘임을 보여줍니다. 많은 사람들은 "리니어 구동"과 "볼 스크류"가 위치 결정도 측면에서 더 우수하다는 인상을 가질 수 있습니다. 그러나 가격, 설계 유연성 및 유지 관리의 용이성은 종종 도입을 고려하는 데 장애가 될 수 있습니다. 반면 타이밍 벨트 및 체인 구동은 비용 이점과 높은 수준의 설계 자유도를 제공하여 도입을 고려하기 쉽습니다. 체인은 금속으로 만들어지고 무겁고 소음이 발생하며 윤활이 필요하다는 단점이 있습니다. 이에 비해 타이밍 벨트는 높은 수준의 위치 결정도가 필요한 기계에 가장 적합한 전달 메커니즘입니다.
이러한 설명에도 타이밍 벨트에 대해 부정적인 인상을 가지고 계신 분이 있을 수 있습니다. 타이밍 벨트인 경우 벨트의 탄성으로 고부하에서의 위치 결정도가 금속 전달 메커니즘보다 떨어질 것이라는 이유입니다. 그러나 최근 발전으로 인해 고부하 타이밍 타이밍 벨트가 개발되고 있으므로 기계 설계 시 옵션으로 검토가 가능합니다.
타이밍 벨트의 위치 결정도에 영향을 미치는 요소는?
코드

위상차에 영향을 미치는 가장 중요한 요소는 코드의 탄성 계수입니다. 벨트에는 동력을 전달하는 "코드"라는 부재가 있으며, 신장률이 낮은 코드(탄성 계수가 높은 코드)는 응답성을 개선하고 위상차를 줄입니다.
① 타이밍 벨트 코드
다음 그래프는 일반적인 타이밍 벨트 코드로 자주 사용되는 글라스 코드(주황색 선)와 탄성 계수가 높은 특징이 있는 카본 코드(회색 선)의 위상차를 비교한 것입니다. 카본 코드가 글라스 코드와 비교해서 구동 시작 시의 진동 폭이 작은 것을 볼 수 있습니다. 즉, 카본 코드는 모터 출력에 더 빨리 응답하고 종동 측으로 동력을 전달하여 최종적으로 위치 결정도가 향상됩니다.
백래시
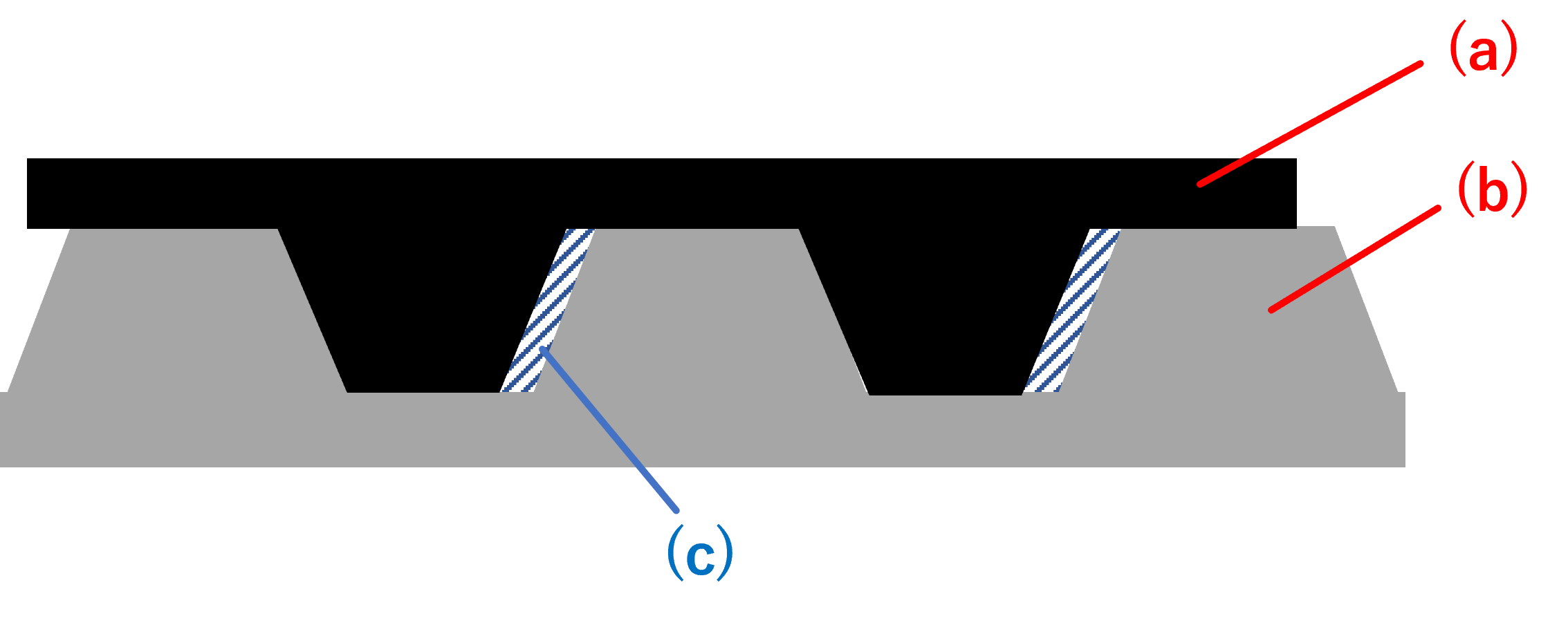
백래시 양은 위치 결정도에 영향을 미치는 또 다른 요소입니다. 백래시는 풀리 이빨과 벨트 이빨 사이의 간격을 말하며, 이 간격의 양을 "백래시 양"이라고 합니다. 백래시가 크면 벨트 시동 시나 역회전 시 구동 풀리와 종동 풀리의 회전에 시간 차이가 발생합니다. 따라서 위치 결정도를 높이기 위해 백래시 양을 가능한 한 작게 해야 합니다.
*(a) 벨트 (b) 풀리 (c) 백래시
백래시 양을 결정하는 가장 중요한 요소는 벨트 이빨 모양입니다. 타이밍 벨트 이빨 모양은 주로 "사다리꼴 치형", "원호 치형" 및 "삼각형 치형"로 분류됩니다.
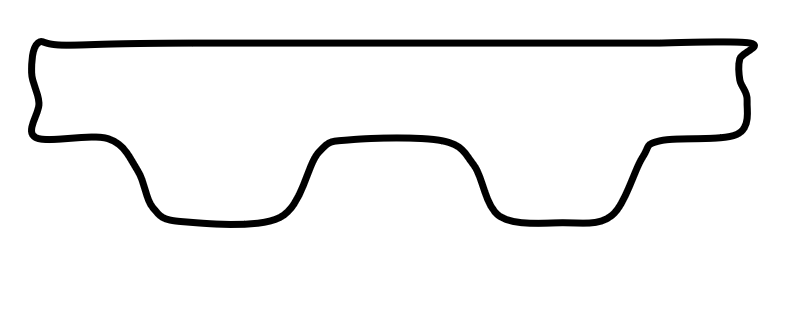
"사다리꼴 치형"은 타이밍 벨트의 초기에 개발된 이빨 모양으로, 풀리와 맞물릴 때 백래시가 크기 때문에 정방향 및 역방향 작동 시 위치 결정도가 비교적 낮습니다.
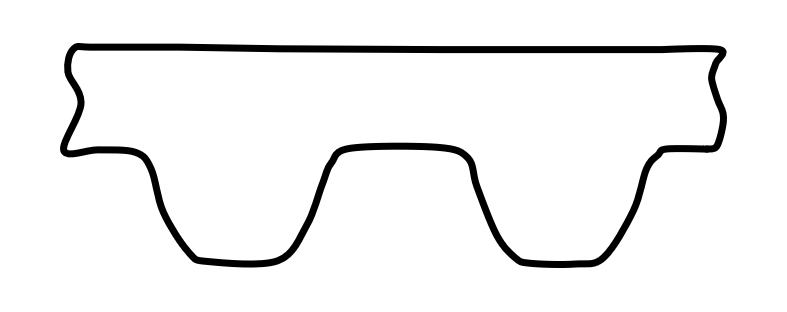
"원호 치형"은 더 높은 위치 정확도, 더 높은 하중 용량 및 더 긴 수명을 위해 설계된 이빨 모양입니다. 원호 치형은 결합을 더 부드럽게 만들고 백래시를 줄입니다. 이 두 가지 효과는 위치 결정도를 개선합니다.
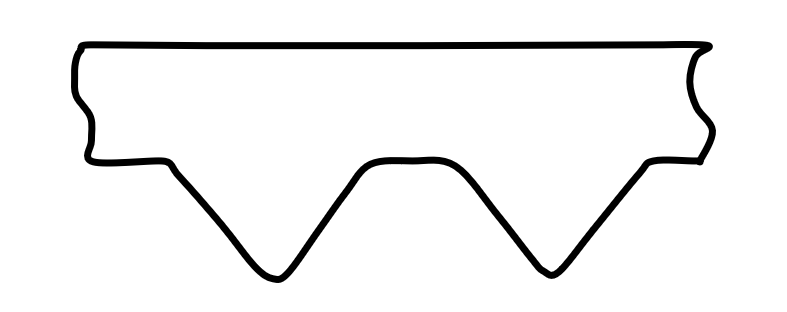
"삼각형 치형"은 풀리에 대해 벨트가 항상 압력면에 접촉하여 맞물리기 때문에 백래쉬가 발생하지 않습니다. 그러나 높은 부하가 걸리게 될 시 치결함이나 이빨 뛰어넘음 등 고장으로 이어질 가능성이 있습니다. 가벼운 하중이 걸리나 높은 위치 결정도가 요구되는 용도에 많이 사용되는 치형입니다.
고정밀 위치 결정에 가장 적합한 벨트는 무엇입니까?
높은 탄성 코드와 원호의 이빨 모양을 가진 벨트가 높은 하중과 하중 변동 조건에서 위상차를 줄이는 데 최적이라는 것을 설명 드렸습니다.
그리고 이러한 조건을 만족하는 타이밍 벨트는 Bando Chemical의 최고급 고하중 타이밍 벨트 Ceptor®-X입니다.
Ceptor®-X는 고탄성 카본 코드를 사용하여 더 나은 응답성과 더 작은 위상 차이를 제공합니다. 또한 원호 사이의 전동 용량이 큰 "S 치형"이 사용됩니다.
Ceptor®-X는 무거운 하중에서도 높은 수준의 위치 결정도가 장기간 실현이 요구되는 곳에 사용되고 있습니다.
또한 폭당 향상된 전동 용량은 동일한 조건에서 표준 S치형의 HP-STS보다 벨트 폭을 40% 더 좁게 만드는 이점이 있습니다. 이를 통해 벨트와 벨트를 받는 풀리의 무게와 공간이 줄어들어 높은 위치 결정도와 경량, 컴팩트한 디자인을 가능하게 합니다.
Ceptor®-X는 주로 산업용 로봇, 의료 및 제약 장비, 반도체 제조 장비, 사출 성형기 등 다양한 응용 분야에서 사용됩니다. 자세한 응용 분야와 예는 이 페이지 하단을 참조하십시오.
요약
전동 메커니즘에서의 위치 결정도의 정의와 높은 수준의 위치 결정도를 달성하기 위한 타이밍 벨트 Ceptor®-X에 대해 설명 드렸습니다. 높은 하중을 받는 메커니즘에서 높은 위치 결정도를 달성하는 데 관심이 있다면 Bando Chemical의 Ceptor®-X를 고려해 보십시오. 궁금한 사항이 있으면 언제든지 문의해 주십시오.